Vehicle electrification has propelled consumer vehicle types into commercial and industrial transportation sectors, forcing continuous development in automotive electronics. While this technology field once focused on entertainment, navigation, and comfort systems, the emphasis has now shifted to high-power, high-voltage, and energy management systems.
These power requirements are not limited to batteries and electric motors; powertrain and power management systems face similar demands. To keep pace with the ever-changing needs of electric vehicles, testing engineers are challenged to stay ahead of trends without purchasing new test equipment every few months.
The DC power supplies, electronic loads, bidirectional power supplies, power analyzers, and voltage testers offered by VASTi Technologies feature flexible capabilities to test multiple devices while still meeting future requirements.
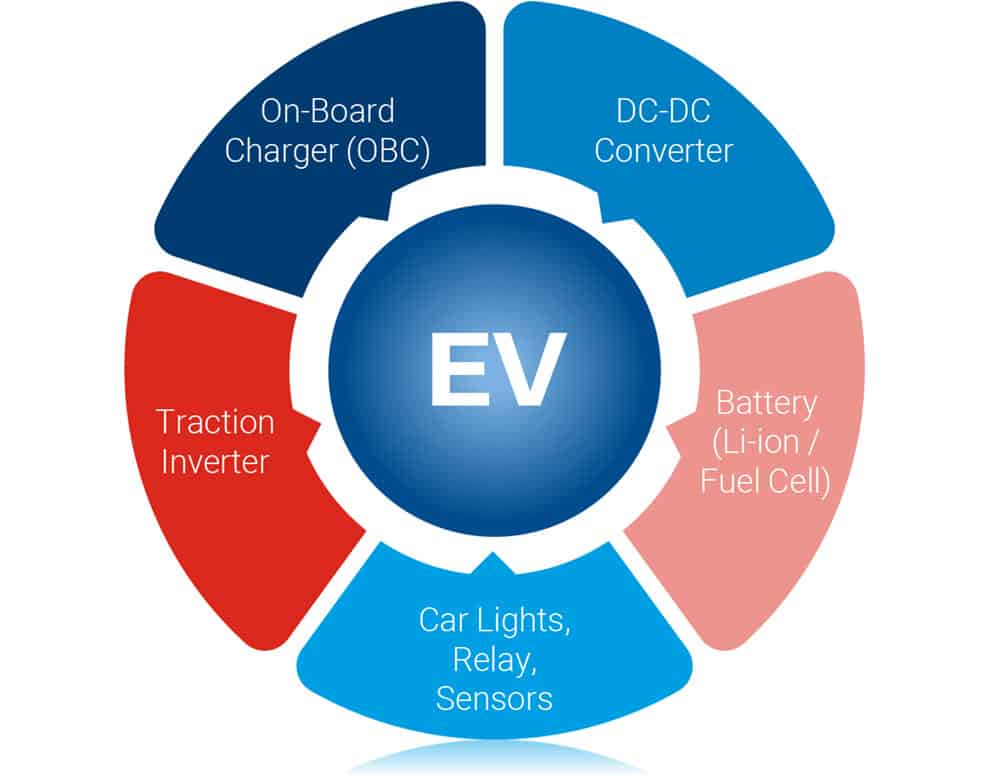
Solutions
Multi-Channel Simultaneous Measurement of Power Component Efficiency
The Vitrek PA900 is a single-unit, four-channel power analyzer designed to test the efficiency of power modules and record parameter variations. Precise and efficient measurements are crucial for electric vehicles, where battery storage capacity is limited. Enhancing the efficiency of power modules can significantly benefit both market growth and technological advancements.
The Vitrek PA900 power analyzer features a Virtual Power Analyzer (VPA) function, which allows multiple PA900 units to be connected in parallel. This capability enables flexible channel selection for calculations, maximizing the utilization of each channel and reducing the cost of purchasing additional instruments.
As shown in the diagram, traditional power analyzers require four units to measure the efficiency of three power modules. In contrast, the PA900 can accomplish the same task with just two units, demonstrating its efficiency and cost-effectiveness.
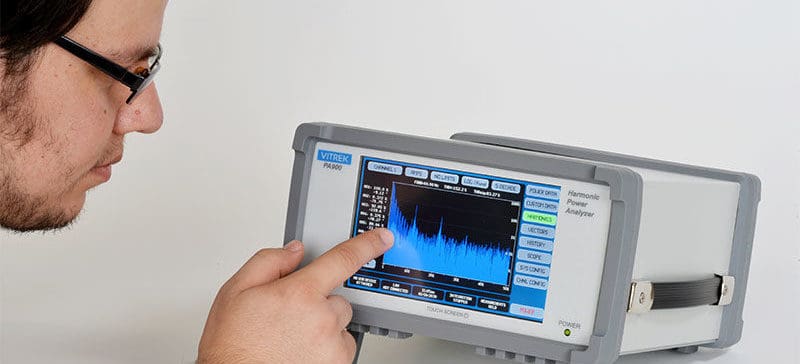
Charging Stations, OBC – Charging System Testing
On-Board Charger (OBC), Plug-in Charging Systems, and Wireless Charger Testing
One of the primary concerns when deciding to purchase an electric vehicle (EV) is how and where to charge it. This issue has spurred the automotive industry to advance different charging concepts to minimize the impact of charging on drivers. This trend appears to be moving towards higher voltages that require smaller currents and less copper. While the industry determines standards, testing these concepts requires a versatile power supply that can meet the low- and high-voltage requirements of many of these chargers.
On-board charger (OBC), plug-in charging system, and wireless charger testing.
DC-DC Converter Testing (DC-DC Inverter)
DC-DC converters in electric vehicles are used to convert the battery voltage (200-800V) to different voltage levels (12V-48V) required by headlights, radios, and other electronic accessories. Testing these converters requires a programmable DC power supply for DC input and an electronic load connected to the DC output.
DC-DC Converter Testing (DC-DC Inverter)
Traction Inverter Testing
In electric vehicles (EVs), the motor is driven by AC power, but most vehicles are powered by DC, which makes sense since the power source is a battery. To facilitate this, inverters are used to convert energy back and forth between the battery and the motor. Traction inverters also support regenerative braking, boosting, and switch protection.
Traction Inverter Testing
Light, relay, sensor, and accessories testing
Besides the main components of electric vehicles, many other parts in both EVs and internal combustion engine vehicles also utilize DC power. Like many components in the vehicle, the voltage required to power them can range from a standard 12V to as high as 1000V or more. Due to this wide variety, test engineers are often forced to purchase several traditional DC power supplies to test everything.
Light, relay, sensor, and accessories testing
Fuel cell, battery, and battery management system testing.
The power sources for electric vehicles include batteries, fuel cells, and battery management systems. Since the electrical demands of various vehicle components are so high, it is essential to test batteries and fuel cells under conditions that simulate the real world. Starting AC power at 100 degrees Fahrenheit, stopping, and commuting during peak hours are all scenarios that EVs encounter on the road, and these scenarios must be recreated to meet various automotive testing standards.
電池模組測試
Fuel Cell Test
Battery Management System Testing
LV 123 Vehicle Test Standard
Automotive Test Standard for BMW, Audi, Daimler, Volkswagen and Porsche
LV123 is a testing standard developed by German automotive original equipment manufacturers (OEMs) for evaluating the electrical characteristics and safety of high-voltage components in road vehicles. These tests are designed to place electrical components in extreme real-world conditions, where the input voltage or demand is either below or above normal operating levels, to ensure the equipment continues to function.
In practice, test engineers must recreate waveforms or test sequences that simulate these extreme conditions to guarantee continuous operation of the product. With the built-in arbitrary waveform and function generator of a programmable DC power supply, you have everything needed to edit precise waveforms that replicate the test requirements outlined in the LV123 standard.
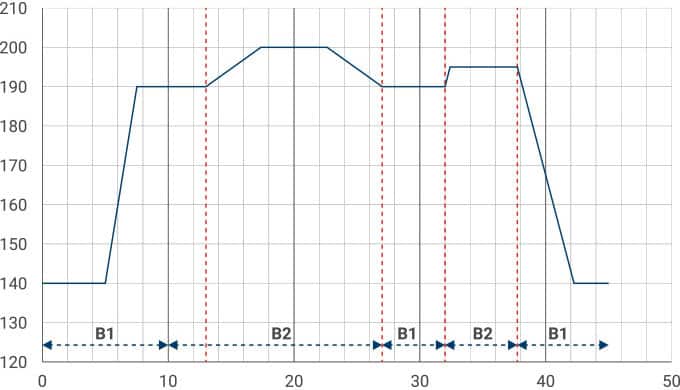
In this scenario, the EA-PSB 9000/10000 series bidirectional DC power supplies can be used to create the test conditions outlined in the LV 123 standard. You can see an example illustration: maximum operational capability.
From the example, it is evident that the PSB can easily and accurately reproduce the specified waveforms. Typically, this type of testing requires the assembly of a specially designed test system. The PSB, however, can directly execute the required power output, loading functionality, and create arbitrary waveforms.
The ability to complete all these tests with a single instrument saves time and cost, and more importantly, significantly reduces the complexity of the testing process.
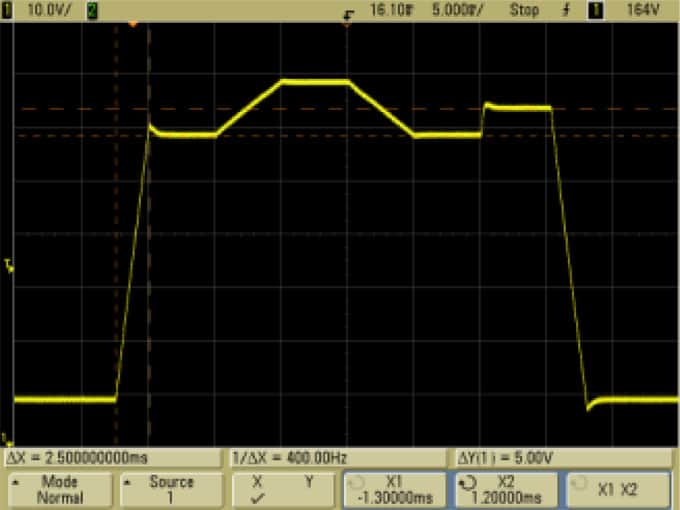